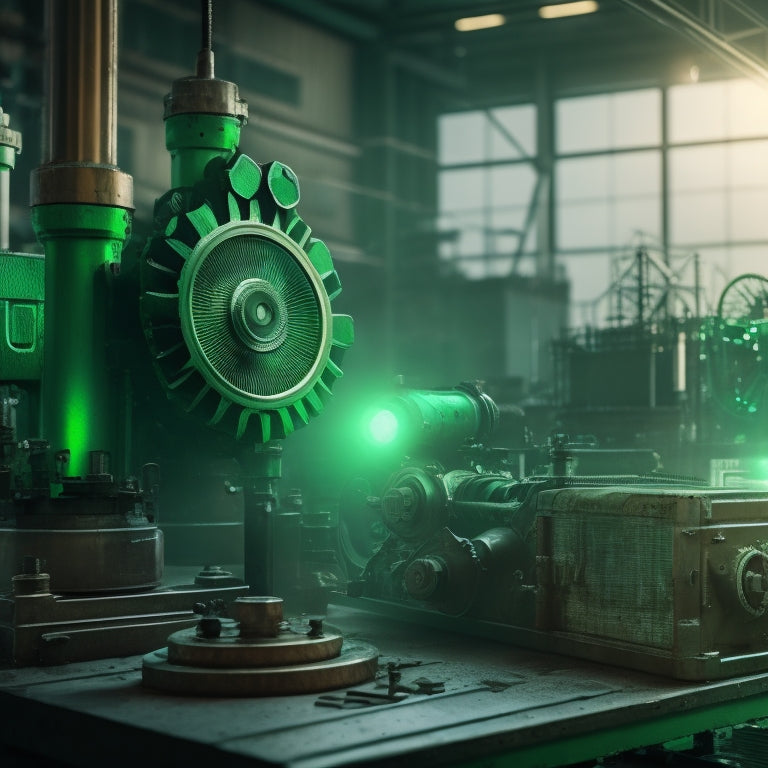
What Drives Down Maintenance Expenses for Business Systems?
Share
By optimizing preventive maintenance schedules, leveraging real-time data analysis, and investing in skilled in-house teams, you can greatly reduce maintenance expenses for your business systems and guarantee top performance. Regularly scheduled maintenance helps identify and address potential issues early, minimizing costly repairs. Proactive monitoring and detection tools help anticipate equipment failures, while skilled teams reduce downtime and increase overall equipment reliability. Standardized procedures and quality installations also play a vital role in driving down maintenance expenses. As you refine your maintenance strategy, you'll uncover even more opportunities to optimize costs and efficiency.
Key Takeaways
• Implementing regular preventive maintenance schedules helps identify and address potential issues early, reducing costly repairs.
• Leveraging proactive monitoring and detection through predictive maintenance tools improves accuracy and optimizes resource allocation.
• Having a skilled in-house maintenance team reduces downtime, increases equipment reliability, and minimizes costly emergency repairs.
• Establishing standardized maintenance procedures ensures consistency, efficiency, and compliance, reducing maintenance expenses.
• Prioritizing quality installation upfront minimizes costly downtime and maintenance, reducing overall expenses.
Regular Preventive Maintenance Schedules
By implementing a regular preventive maintenance schedule, you can identify and address potential issues before they escalate into major problems that disrupt business operations. This proactive approach enables you to allocate resources more efficiently, reducing downtime and minimizing the likelihood of costly repairs.
To maximize the effectiveness of your maintenance schedule, it's crucial to determine the best maintenance frequency for each system or asset. This may involve consulting with maintenance personnel to assess the condition and usage of each component. By doing so, you can prioritize tasks, allocate resources, and make sure that critical systems receive the necessary attention to prevent failures.
Proactive Monitoring and Detection
As you shift your focus to proactive monitoring and detection, you'll want to leverage real-time data analysis to identify potential issues before they escalate into costly problems.
By implementing predictive maintenance tools, you can analyze equipment performance data and detect anomalies that may indicate impending failures.
Real-time Data Analysis
You can detect potential issues before they cause downtime by leveraging real-time data analysis to proactively monitor your business systems and detect anomalies as they occur. This proactive approach enables you to take corrective action before problems escalate, reducing downtime and maintenance expenses.
Real-time data analysis allows you to visualize system performance in real-time, identifying trends and patterns that may indicate potential issues. This enables you to pinpoint areas where automation opportunities exist, streamlining processes and optimizing system performance.
With data visualization, you can quickly identify areas of concern, making data-driven decisions to mitigate potential issues before they become major problems. By leveraging real-time data analysis, you'll be better equipped to control and optimize your business systems, driving down maintenance expenses and maximizing uptime.
Predictive Maintenance Tools
To take proactive monitoring and detection to the next level, implement predictive maintenance tools that can learn from your real-time data, identifying patterns and anomalies to anticipate equipment failures before they happen. These tools utilize Machine Learning algorithms to analyze your data, enabling you to take proactive measures to prevent downtime.
By integrating Digital Twins, you can create virtual replicas of your equipment, allowing you to simulate scenarios, test hypotheses, and refine your maintenance strategies.
Some key benefits of predictive maintenance tools include:
-
Improved accuracy: by leveraging Machine Learning and real-time data, you can reduce false positives and negatives.
-
Enhanced foresight: anticipate equipment failures with confidence, allowing you to schedule maintenance during planned downtime.
-
Optimized resource allocation: allocate resources more efficiently, reducing waste and maximizing productivity.
Skilled In-House Maintenance Teams
Having a skilled in-house maintenance team on site can greatly reduce downtime and increase overall equipment reliability, allowing your business to minimize costly repairs and maintain peak production levels.
By investing in your team's development, you'll see improvements in team dynamics, leading to more efficient collaboration and issue resolution. Consider allocating a dedicated training budget to upskill your team in specialized areas, such as advanced troubleshooting or equipment-specific maintenance.
This investment will pay off in the long run, as your team becomes more self-sufficient and capable of tackling complex issues in-house. With a skilled team, you'll reduce your reliance on external contractors and minimize the need for costly emergency repairs.
Standardized Maintenance Procedures
By establishing standardized maintenance procedures, your organization can guarantee consistency and efficiency in equipment upkeep, reducing the likelihood of human error and minimizing downtime. This approach enables you to streamline maintenance tasks, ensuring that all technicians follow the same procedures, thereby reducing variability and potential mistakes.
To achieve best results, consider the following:
-
Implement procedure compliance checks to make sure that all maintenance tasks are completed correctly and on time.
-
Automate repetitive tasks where possible, freeing up technicians to focus on more complex issues.
-
Develop a detailed maintenance schedule, outlining specific tasks, frequencies, and responsible personnel.
Quality of Installation Matters
You'll greatly reduce the likelihood of equipment failure and subsequent maintenance needs if you make sure that all business systems are installed correctly from the start. Proper installation is vital, as it sets the foundation for a system's performance and reliability.
Guarantee that your installation team receives proper training to ensure that all components are installed correctly and configured accurately. Additionally, prioritize clean cabling to prevent damage, signal degradation, and electromagnetic interference.
A well-planned and executed installation will minimize the risk of costly downtime and maintenance, giving you more control over your business operations. By investing time and effort upfront, you'll reap the benefits of reduced maintenance expenses and optimized system performance.
Manufacturer Support and Warranties
When purchasing business systems, be sure to meticulously evaluate the manufacturer's support options and warranty terms to make certain you have adequate protection against unexpected maintenance costs. You want to confirm that you're covered in case something goes wrong, and that you're not stuck with a hefty repair bill.
Some key things to look for include:
-
Extended coverage options that provide additional protection beyond the standard warranty period
-
Premium services that offer priority support and faster response times
-
Clear and transparent warranty terms that outline exactly what's covered and for how long
Frequently Asked Questions
How Do I Prioritize Maintenance Tasks for Multiple Systems Simultaneously?
'When prioritizing maintenance tasks for multiple systems, you'll need to assess resource allocation and system interdependence. Identify critical systems, allocate resources accordingly, and schedule tasks to minimize downtime and guarantee seamless system integration.'
Can Maintenance Expenses Be Capitalized or Must They Be Expensed?
'Fast-forward to the future, where maintenance expenses meet accounting rules! You'll find that some can be capitalized as a Capital Expenditure, while others are expensed; it's essential to understand the distinction to optimize your financial strategy.'
Are There Any Tax Benefits to Investing in Maintenance Activities?
You can leverage tax incentives and depreciation savings by investing in maintenance activities, as some expenses are eligible for accelerated depreciation, reducing your taxable income and boosting your bottom line.
How Do I Measure the ROI of Maintenance Cost Reductions?
"When you're trying to measure the ROI of maintenance cost reductions, think of it like tuning a car engine - every tweak has a ripple effect. You'll want to track Cost Savings and key Financial Metrics, like mean time between failures (MTBF), to see how your efforts pay off."
Can Maintenance Expenses Be Reduced Without Sacrificing System Performance?
You can reduce maintenance expenses without sacrificing system performance by implementing system optimization strategies, such as streamlining workflows and consolidating systems, and conducting thorough cost analysis to identify areas for improvement.
Related Posts
-
Evaluating Solar Power Options for Businesses
Evaluating solar power options for your business can greatly reduce energy costs and enhance sustainability. Start by...
-
How to Reduce Home Energy Bills
To reduce your home energy bills, start by investing in energy-efficient appliances and upgrading your insulation. Lo...
-
Comparative Analysis of Top Solar Brands
To conduct a comparative analysis of top solar brands, focus on key metrics like durability, energy efficiency, and s...