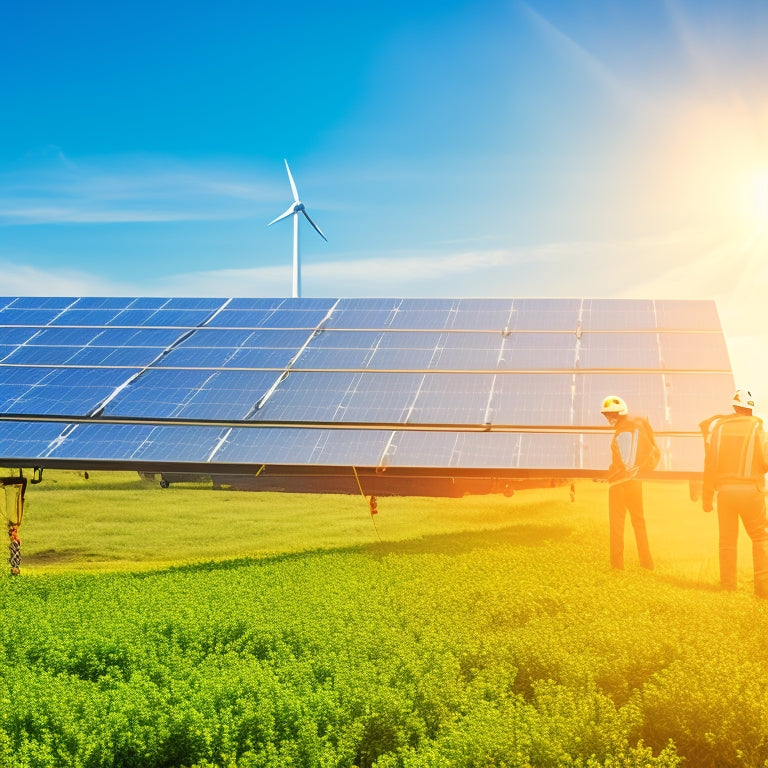
Maximize Energy Output With Regular Inspections
Share
Maximize your energy output by conducting regular inspections. Early detection identifies potential issues before they escalate, maintaining peak efficiency. Advanced diagnostics and predictive analytics forecast component degradation, allowing proactive maintenance. Routine cleaning and calibration based on real-time data prevent obstructions and guarantee systems operate at peak performance. Regular assessments extend the lifespan and reliability of your equipment, leading to significant energy savings and cost reductions. Implement structured inspection routines to collect valuable data, helping you spot minor defects early. By integrating thorough inspection protocols, you'll achieve significant improvements in energy efficiency and system resilience. Explore advanced techniques and insights for further optimization.
Key Takeaways
- Regular inspections identify and address minor issues promptly to prevent performance dips.
- Routine cleaning and maintenance prevent obstructions and ensure optimal energy output.
- Predictive analytics during inspections forecast component degradation and maintain efficiency.
- Structured inspections provide valuable performance data for continual system calibration.
- Early detection of material degradation during inspections extends system lifespan and efficiency.
Identify Potential Issues Early
https://www.youtube.com/watch?v=nZF0UXh7GT0
Regular inspections help you identify potential issues early, preventing costly repairs and downtime. By leveraging predictive analytics, you can forecast component degradation before it impacts your system's performance. This proactive approach empowers you to address minor problems before they escalate into significant failures.
Predictive analytics uses data from past inspections and real-time monitoring to predict when a component might fail. You can analyze trends and patterns, thereby identifying early signs of wear and tear. This method not only saves you from unexpected breakdowns but also optimizes your maintenance schedule, guaranteeing that repairs are done at the most convenient times.
Component degradation often starts subtly, making it easy to overlook without regular inspections. By incorporating predictive analytics into your routine, you can detect these minute changes. This foresight allows you to replace or repair parts before they compromise your system's integrity.
Ultimately, regular inspections combined with predictive analytics provide you with the freedom to operate without constant fear of sudden malfunctions. You gain control over your maintenance activities, enabling a more efficient, reliable system. This strategic approach ensures longevity and peak performance, aligning with your goal of maximizing energy output.
Maintain Optimal Efficiency
To maintain peak efficiency, you must continually calibrate and fine-tune your equipment based on real-time performance data. By doing so, you guarantee that each component operates at its highest potential, preventing energy loss and optimizing output.
Start by instituting a schedule for routine cleaning to remove dust, debris, and other contaminants that can obstruct performance. Clean surfaces and internal parts regularly to maintain peak airflow and functionality.
Vital management is essential for keeping your equipment running efficiently. Excess heat can lead to decreased performance and increased wear. Implement cooling systems, such as fans or liquid cooling, to dissipate heat effectively. Monitor thermal sensors closely and adjust settings as needed to maintain the ideal operating temperature.
Utilize predictive analytics to anticipate performance dips and address them proactively. By analyzing trends and patterns, you can make informed decisions about when to perform maintenance tasks. This approach minimizes downtime and maximizes energy output.
Extend System Lifespan
Regular inspections help prevent costly breakdowns and identify wear early, extending your system's lifespan.
By addressing minor issues before they escalate, you avoid significant repairs and downtime.
This proactive approach guarantees that your equipment operates efficiently over a longer period.
Prevent Costly Breakdowns
Consistent inspections identify potential issues early, preventing costly breakdowns and extending the system's lifespan. By implementing preventive maintenance, you can spot minor defects before they escalate into major problems. This proactive approach not only wards off unexpected failures but also saves you significant repair costs. Cost avoidance becomes a tangible benefit, freeing up resources for other critical investments.
When you regularly inspect your systems, you're empowering yourself to maintain peak performance. Technical assessments allow you to fine-tune components, ensuring they operate efficiently. This diligence minimizes wear and tear, reducing the likelihood of sudden malfunctions. The result? Enhanced reliability and a longer operational life for your equipment.
Moreover, a structured inspection regime provides valuable data on system performance. By analyzing this data, you can make informed decisions about upgrades and replacements, further optimizing your setup. Investing time in these inspections translates to fewer disruptions and sustained productivity.
Embrace the freedom that comes with a well-maintained system. You'll not only sidestep expensive repairs but also enjoy uninterrupted service. Preventive maintenance is more than a cost-saving measure; it's a strategy for extending the lifespan of your investments and maximizing their output.
Identify Wear Early
Spotting wear early enables you to address issues before they compromise the system's functionality and longevity. By regularly inspecting your system, you identify signs of material degradation and component fatigue. Early detection gives you the ability to replace or repair parts before they fail, ensuring continuous operation and maximizing energy output.
Material degradation often manifests as cracks, corrosion, or wear that reduces the structural integrity of components. When left unchecked, these issues can lead to catastrophic failures. Regular inspections help you detect these problems early, allowing for timely interventions that extend the system's lifespan.
Component fatigue occurs when parts are subjected to repeated stress, leading to tiny fractures that can grow over time. Identifying these fractures early through techniques like non-destructive testing (NDT) ensures you address them before they result in failure. This proactive approach not only minimizes downtime but also optimizes the performance of your system.
Increase Energy Savings
You can increase energy savings by ensuring efficient system performance through regular inspections.
These inspections help you detect issues early, preventing costly inefficiencies.
Efficient System Performance
Regular inspections guarantee that your system operates at peak efficiency, leading to significant energy savings. By leveraging innovative technology and advanced diagnostics, you secure each component functions at its best. Efficient system performance isn't just about reducing energy use; it's about freeing yourself from unnecessary costs and environmental impact.
Advanced diagnostics provide real-time data, allowing you to pinpoint inefficiencies swiftly. This proactive approach means you can address minor issues before they escalate into costly problems. Innovative technology, such as smart sensors and automated monitoring systems, continuously assesses your system's performance, providing actionable insights without manual intervention.
Regular inspections also help you maintain system components in top condition. Clean filters, well-lubricated parts, and calibrated sensors work together to ensure minimal energy wastage. When every part of your system performs efficiently, you maximize output while minimizing energy consumption.
Incorporating these strategies into your maintenance routine guarantees that you're not just saving energy but also extending your system's lifespan. The result? You achieve a sustainable, cost-effective operation that aligns with your goals for efficiency and environmental stewardship. By prioritizing regular inspections, you unleash the full potential of your system and pave the way for long-term energy savings.
Early Issue Detection
Identifying issues early not only guarantees efficient system performance but greatly boosts energy savings by preventing minor problems from escalating. By leveraging advanced techniques like thermal imagery and acoustic monitoring, you can pinpoint potential failures before they become critical. Thermal imagery helps you detect abnormal heat patterns indicative of electrical faults or insulation failures, while acoustic monitoring identifies irregular vibrations and noises, signaling mechanical wear or misalignment.
Implementing these technologies in your regular inspection routine empowers you to act proactively. Thermal imagery allows you to visualize unseen thermal anomalies, enabling targeted maintenance. This minimizes downtime and ensures peak energy use. Acoustic monitoring, on the other hand, provides real-time data on the health of your equipment. By analyzing sound frequencies, you can diagnose issues such as bearing failures or air leaks, addressing them before they affect system efficiency.
Incorporating early issue detection into your maintenance strategy enhances your control over energy costs. You're not just fixing problems; you're preventing them. This proactive approach liberates you from unexpected breakdowns and costly repairs, ultimately maximizing your energy output and savings.
Optimal Resource Utilization
Maximizing energy savings hinges on the strategic allocation and efficient use of available resources. To achieve this, you must conduct a thorough energy audit. This process allows you to identify how and where energy is consumed and uncover inefficiencies that drain resources.
With detailed insights from the audit, you can make informed decisions on resource allocation, directing energy towards high-return areas.
Prioritizing resource allocation involves optimizing systems and processes to reduce waste. For example, upgrading to energy-efficient lighting and HVAC systems can greatly lower consumption. It's essential to continuously monitor energy usage patterns to adapt and refine your strategy. Implementing smart sensors and automation can provide real-time data, enabling you to react swiftly to any anomalies.
Another key aspect of efficient resource utilization is employee engagement. Educate your team on energy-saving practices and encourage a culture of mindfulness regarding energy use. This collective effort can significantly enhance your overall savings.
Ultimately, efficient resource allocation and regular energy audits are essential for maximizing energy output. By embracing these practices, you'll not only reduce costs but also contribute to a more sustainable and liberated energy future.
Ensure Safety Standards
Conducting thorough inspections guarantees that all safety standards are met, preventing potential hazards and maintaining peak energy output. By adhering to strict safety protocols and ensuring regulatory compliance, you'll not only safeguard your equipment but also protect your team from potential dangers. Regular inspections allow you to identify and rectify issues before they escalate, ensuring a seamless and efficient operation.
To evoke a sense of responsibility and urgency, consider the following:
- Reduce the risk of catastrophic failures
- Protect employees from workplace accidents
- Prolong the lifespan of critical equipment
- Avoid costly downtime and repairs
- Maintain a reputation for safety and reliability
When you implement thorough safety checks, you're not just ticking boxes for regulatory compliance. You're actively creating a secure environment where your team can focus on maximizing energy output without fear. This approach embodies a proactive, rather than reactive, mindset—essential for anyone looking to break free from inefficiencies and ensure top-notch performance.
Optimize Power Output
To optimize power output, you need to perform regular equipment performance checks and make necessary calibrations and adjustments. These actions guarantee that your machinery operates at peak efficiency.
Don't overlook these critical steps to maintain and enhance energy production.
Equipment Performance Checks
Regular equipment performance checks are essential to guarantee that power output remains optimized and efficient. By conducting these checks, you secure that your systems operate at peak performance, reducing downtime and increasing productivity.
Leveraging remote diagnostics can greatly enhance these checks, allowing for real-time monitoring and immediate identification of issues without the need for on-site intervention.
To fully capitalize on the benefits of performance checks, incorporate thorough training programs for your team. These programs will empower your staff with the knowledge and skills necessary to perform detailed inspections and utilize diagnostic tools effectively.
Consider the following benefits of regular equipment performance checks:
- Increased Reliability: Detect potential issues before they lead to system failures.
- Cost Savings: Minimize expensive repairs and replacements by addressing problems early.
- Enhanced Efficiency: Ensure that machinery operates at the best levels, conserving energy.
- Extended Equipment Lifespan: Regular maintenance extends the life of your equipment.
- Operational Freedom: Reduce unexpected downtimes, giving you greater control over your operations.
Calibration and Adjustments
Building on the foundation of regular equipment performance checks, precise calibration and timely adjustments are key to optimizing power output.
To achieve peak efficiency, you must focus on sensor calibration and instrument alignment. Accurate sensor calibration guarantees that all measurements reflect true operating conditions, eliminating discrepancies that could lead to suboptimal performance. Regularly calibrate sensors to maintain their accuracy, particularly in environments subject to temperature fluctuations or mechanical vibrations.
Instrument alignment is equally critical. Proper alignment minimizes energy losses due to misaligned components. This process involves adjusting the position of various instruments to ensure they operate in harmony. Misalignment can cause friction, wear, and inefficiencies that degrade overall system performance.
Prevent Costly Repairs
Identifying potential issues early through regular inspections can greatly reduce the likelihood of expensive repairs. When you catch problems before they escalate, you not only save money but also avoid the stress and downtime associated with major repairs. Regular inspections can help maintain your insurance coverage and validate contractor warranties, making sure you're financially protected.
Consider the emotional and financial impact of unanticipated repairs. Here's what you can avoid with regular inspections:
-
Unexpected breakdowns: Catching small issues early prevents sudden, costly failures.
-
Extended downtime: Regular checks make certain your equipment runs smoothly, minimizing operational interruptions.
-
Warranty voidance: Failing to inspect regularly can void contractor warranties, leaving you to foot the bill.
-
Insurance issues: Insurers might deny claims if you neglect routine inspections, leading to out-of-pocket expenses.
-
Energy inefficiency: Poorly maintained equipment consumes more energy, increasing operational costs.
Verify Proper Installation
Ensuring your equipment is installed correctly is the next step in maximizing energy output and avoiding future complications. Proper installation methods are essential for the efficiency and longevity of your energy systems. Begin by thoroughly reviewing the manufacturer's guidelines. These documents offer precise instructions tailored to your specific equipment, ensuring each component is assembled and positioned as intended.
Conduct a meticulous setup verification. Check every connection, bolt, and alignment. Pay attention to electrical wiring, as improper connections can lead to significant energy losses or even hazardous conditions. Utilize diagnostic tools to verify that all components are communicating correctly and operating within their best parameters.
Don't overlook environmental factors during installation. Ensure your equipment is shielded from elements that could impact performance, such as excessive dust, moisture, or temperature fluctuations. These factors can degrade components over time, reducing efficiency and increasing maintenance needs.
Monitor Performance Trends
By regularly monitoring performance trends, you can quickly identify inefficiencies and optimize your energy systems for peak output. Utilizing data analysis, you'll uncover critical insights into how your system performs under various conditions. Trend visualization tools can help you understand these patterns, enabling proactive adjustments that prevent energy loss and enhance efficiency.
To effectively monitor performance trends, consider the following:
-
Real-time monitoring: Keep a constant eye on your system's performance to catch issues as they arise.
-
Historical data comparison: Analyze past performance data to identify recurring problems and long-term trends.
-
Anomaly detection: Use algorithms to pinpoint deviations from normal operating conditions.
-
Predictive maintenance: Forecast potential issues before they become significant problems, reducing downtime.
-
Performance benchmarking: Compare your system's performance against industry standards to make sure you're maximizing efficiency.
Harnessing the power of data analysis and trend visualization liberates you from reactive maintenance, allowing you to preemptively address inefficiencies. With a detailed understanding of your system's performance trends, you can make informed decisions that optimize energy output.
This approach not only increases efficiency but also empowers you to maintain control over your energy systems, making certain they operate at their absolute best.
Enhance Resale Value
Wondering how regular inspections can enhance your system's resale value? Consistent check-ups guarantee your energy system operates at peak efficiency, directly boosting your property's curb appeal. A well-maintained system signals reliability and reduced future costs, driving up market demand. Buyers are wary of potential hidden issues; you can alleviate these concerns with a documented history of regular inspections.
Here's a quick breakdown of benefits:
Feature | Benefit |
---|---|
Improved Efficiency | Lower energy bills, attracting buyers |
Recorded History | Trust and transparency |
Minimized Repairs | Fewer surprises for potential buyers |
Attractiveness | Increased market demand |
Regular inspections also identify minor issues before they escalate, maintaining the system's top performance. This proactive approach extends the lifespan of your energy system, translating into better resale value. Buyers appreciate the foresight and diligence, often translating into a quicker sale at a higher price.
In a competitive market, having an edge matters. By ensuring your system is in top shape, you not only save on immediate operational costs but also position your property as a prime choice for energy-conscious buyers. Regular inspections are a strategic move to maximize your investment's return.
Frequently Asked Questions
How Often Should Energy Systems Be Inspected?
To determine the ideal inspection frequency, consult your system's maintenance schedule. Typically, energy systems require inspections every six months. Regular checks guarantee efficiency and prevent issues, granting you the freedom from unexpected downtime.
Are Professional Inspections More Effective Than DIY Checks?
Yes, professional inspections are more effective than DIY checks. They use advanced inspection tools, minimizing DIY risks. By trusting experts, you guarantee precision and safety, liberating yourself from potential errors and suboptimal energy output.
What Qualifications Should an Energy Inspector Have?
Your energy inspector should meet certification requirements and have a solid experience level. Look for credentials like BPI or RESNET certification, ensuring they've got practical experience to perform accurate, efficient inspections, freeing you from energy inefficiencies.
How Do Weather Conditions Affect Inspection Schedules?
Seasonal variations and extreme weather have a considerable impact on inspection schedules. You'll need to adjust inspections more frequently during harsh conditions to guarantee safety and efficiency. Plan proactively to mitigate risks and maintain peak energy output throughout the year.
Can Regular Inspections Help in Identifying Energy Theft or Misuse?
Can you imagine the freedom of knowing your energy is used efficiently? Regular inspections, through energy audits, can pinpoint discrepancies in usage patterns, helping you identify and prevent energy theft or misuse. Embrace control and efficiency!
Related Posts
-
Steps to Prepare for Solar Installation
To prepare for solar installation, start by evaluating your current energy consumption and future needs to determine ...
-
How to Finance Home Solar Panels
Financing home solar panels offers several strategies to lighten your initial costs while maximizing long-term benefi...
-
Solar Inverter Troubleshooting for Beginners
Troubleshooting your solar inverter starts with understanding its efficiency and performance metrics. Check for prope...