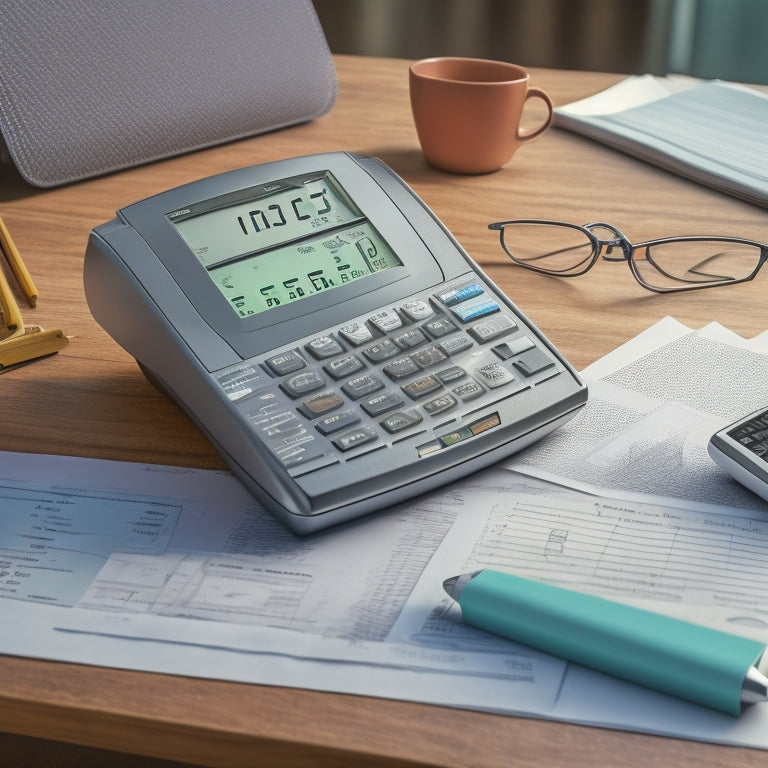
Average Annual Maintenance Costs for Business Panels
Share
You can expect to allocate around 3-5% of your business panel's total investment towards average annual maintenance costs, broken down into various expenditure categories. Routine tasks like lubrication and inspections make up 30-40% of total maintenance costs, while repairs and replacements constitute around 20-30%. Inverter maintenance, cleaning, and performance monitoring also factor into your overall maintenance budget. By understanding these costs, you'll be better equipped to plan and manage your maintenance expenses. As you explore the specific costs involved, you'll uncover more insights to optimize your business panel's performance and efficiency.
Key Takeaways
• Routine maintenance tasks, like lubrication and cleaning, account for 30-40% of total maintenance costs and prevent equipment failures.
• Repairs and replacements make up 20-30% of maintenance expenditure, with 1-2% of panels requiring replacement annually.
• Inverter maintenance and upkeep fees average 5-10% of total maintenance expenditure and ensure peak energy efficiency.
• Cleaning and inspection expenses make up 3-5% of maintenance costs, preventing debris buildup and energy losses.
• Performance monitoring and analysis costs average 5-10% of maintenance expenditure, enabling real-time tracking and optimization of energy production.
Scheduled Maintenance Expenditure Breakdown
Your scheduled maintenance expenditure breakdown typically consists of routine tasks, such as lubrication, cleaning, and inspections, which account for approximately 30-40% of your total maintenance costs. These tasks are vital for preventing equipment failures and reducing downtime.
When allocating your budget, it's important to prioritize these routine tasks to guarantee your business panel runs smoothly. Effective financial planning is key to maintaining a healthy budget allocation. By setting aside a dedicated amount for scheduled maintenance, you'll avoid unexpected expenses and minimize the risk of costly repairs.
Typical Repair and Replacement Costs
When equipment failures do occur, you'll need to budget for repairs and replacements, which can account for around 20-30% of your total maintenance expenditure.
Panel failure rates vary, but on average, you can expect around 1-2% of your panels to fail annually. Fortunately, many manufacturers offer warranty coverage for their products, which can help mitigate some of these costs. However, it's essential to review your warranty terms carefully to understand what's covered and for how long.
Additionally, you should also factor in the cost of replacement parts, labor, and any necessary upgrades. By understanding these costs, you can better manage your maintenance budget and minimize downtime.
Inverter Maintenance and Upkeep Fees
About 5-10% of your total maintenance expenditure goes towards inverter maintenance and upkeep fees, which can add up quickly if you don't keep a close eye on them. You'll want to prioritize inverter reliability to guarantee your business panels are running at peak energy efficiency.
Regular maintenance helps prevent unexpected downtime and reduces the risk of costly repairs. By investing in routine inverter maintenance, you'll enjoy improved system performance, reduced energy losses, and a longer lifespan for your inverters.
Don't overlook these essential fees, as they're vital for maintaining your system's overall health and performance. By staying on top of inverter maintenance, you'll reap the benefits of a well-functioning system that saves you time, money, and resources in the long run.
Cleaning and Inspection Expenses
Regular cleaning and inspection of your business panels are crucial to preventing debris buildup, maintaining peak energy output, and extending the lifespan of your system. Cleaning and inspection expenses account for around 3-5% of your total maintenance expenditure.
You'll need to budget for regular debris removal, which helps prevent energy losses and reduces the environmental impact of your business. Inspection costs will vary depending on the frequency and type of inspections you require.
On average, you can expect to pay between $500 and $2,000 per year for cleaning and inspection services, depending on the size and complexity of your system. By staying on top of cleaning and inspection, you'll minimize downtime, maximize energy production, and ensure a longer lifespan for your business panels.
Performance Monitoring and Analysis Costs
Track your business panel's performance in real-time to identify areas of improvement and optimize energy production, with performance monitoring and analysis costs averaging around 5-10% of your total maintenance expenditure. This cost includes the tools and software you use to monitor your panel's performance. With real-time tracking, you can identify issues before they become major problems, reducing downtime and increasing energy production.
Here are some ways you can utilize performance monitoring and analysis:
-
Data Visualization:
Use interactive dashboards to visualize your panel's performance, making it easier to identify trends and patterns. -
Real-time Tracking:
Monitor your panel's energy production in real-time, allowing you to respond quickly to any issues that arise. -
Predictive Maintenance:
Use data analysis to predict when maintenance is required, reducing the likelihood of unexpected downtime.
Frequently Asked Questions
What Are the Benefits of Regular Maintenance for Business Panels?
"You're probably thinking, 'Why waste time on maintenance when everything's running smoothly?' But, by doing so, you'll actually increase efficiency, reduce downtime, and avoid costly surprises, giving you more control over your business's operations and bottom line."
Can I Perform Maintenance Tasks In-House or Outsource Them?
You can decide whether to perform maintenance tasks in-house, relying on your staff's expertise, or outsource them to a reliable vendor, ensuring timely and efficient service, depending on your business needs and resources.
How Do I Determine the Maintenance Budget for My Panels?
You'll determine your maintenance budget for business panels by factoring in regular panel inspection costs, allocating funds for potential repairs, and considering your budget allocation strategy to make sure you're prepared for unexpected expenses.
What Kind of Maintenance Is Required for Energy Storage Systems?
You'll need to perform regular battery calibration to guarantee peak energy storage system performance, and conduct system monitoring to identify potential issues before they escalate, allowing you to take proactive control of your energy storage.
Are There Any Government Incentives for Panel Maintenance Costs?
You'll be glad to know that, yes, there are government incentives for panel maintenance costs! For instance, in the US, you can claim 30% Tax Credits for renewable energy projects, and even explore Renewable Grants like the USDA's Rural Energy for America Program.
Related Posts
-
Solar Power for Reducing Carbon Footprint
Solar power is an effective strategy for reducing your carbon footprint. By adopting solar energy, you can cut greenh...
-
Off-Grid Solar Solutions for Eco-Conscious Businesses
Off-grid solar solutions offer you a path to both sustainability and substantial cost savings. By adopting these syst...
-
Passive Solar Design Strategies for Homes
To effectively implement passive solar design strategies in your home, focus on ideal building orientation and strate...